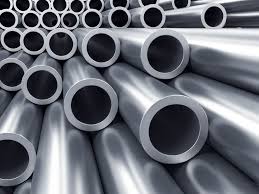
Choosing the right aluminum extrusion factory is a critical decision that can significantly impact the success of your project—whether you’re designing complex aerospace components, lightweight automotive frames, solar mounting structures, or architectural systems. The wrong partner can lead to costly delays, subpar quality, and inefficiencies, while the right one can bring your vision to life with precision, durability, and efficiency.
In this in-depth guide, we’ll walk you through everything you need to know to make an informed decision when selecting an aluminum extrusion factory for your next project.
Understanding the Aluminum Extrusion Process
Before diving into the selection criteria, it’s important to understand what aluminum extrusion factory entails.
Aluminum extrusion is the process of shaping aluminum by forcing it through a die to create objects with a specific cross-sectional profile. This technique is widely used because it allows for the production of complex, lightweight, and durable shapes that are perfect for countless industrial applications.
The process involves:
Heating the aluminum billet
Pushing it through a precision die
Cooling, stretching, and cutting the extruded profile
Finishing processes such as anodizing, powder coating, or machining
It’s a cost-effective, energy-efficient, and highly customizable manufacturing method. But achieving consistently high-quality results depends heavily on choosing the right factory.
Key Factors to Consider When Choosing an Aluminum Extrusion Factory
1. Technical Expertise and Industry Experience
Start by evaluating the factory’s technical capabilities and years of experience. A seasoned aluminum extrusion factory will understand the nuances of various industries, including automotive, construction, electronics, and aerospace. Their familiarity with material behaviors, extrusion tolerances, and alloy selection can save you from costly mistakes.
Ask:
How long have they been in operation?
Do they specialize in specific industries?
Can they offer case studies or past project examples?
2. Range of Extrusion Capabilities
Not all factories have the same machinery or output capabilities. You’ll want to ensure the factory has the capacity to produce your required profile shapes, sizes, and volumes.
Key considerations:
Press tonnage – Higher tonnage allows for larger or more complex profiles.
Maximum profile dimensions – Does the factory support your design?
Wall thickness tolerance – Are they able to maintain precision?
Minimum order quantities – Can they handle small-batch prototyping or high-volume runs?
3. In-House Die Design and Tooling
Die design is a crucial part of aluminum extrusion. A factory with in-house die-making capabilities can drastically reduce lead time, facilitate better communication, and offer design improvements that reduce material waste or improve profile performance.
Benefits of in-house tooling:
Faster turnaround
Lower costs
Greater customization
Easy revisions if design changes are needed
Be sure to ask if the factory uses CAD/CAM systems, how long die creation takes, and what maintenance or storage options are offered for custom dies.
4. Alloy Options and Material Quality
Different aluminum alloys offer different mechanical properties, corrosion resistance, and thermal conductivity. A good extrusion partner will offer a wide range of alloys and help you select the most suitable one based on your project’s requirements.
Common alloys:
6063 – Architectural grade, excellent finish and corrosion resistance
6061 – Strong, versatile, good for structural use
6082 – High strength, good machinability
7075 – Aerospace-grade, high strength-to-weight ratio
Also ask:
Where is their aluminum sourced from?
Do they offer recycled or eco-friendly options?
Are they certified to meet standards like ASTM, RoHS, or ISO?
5. Finishing Services and Post-Processing
Your project may require more than just raw extrusions. A full-service extrusion factory should offer value-added services such as:
Anodizing
Powder coating
Polishing or brushing
Cutting and machining
Drilling, tapping, or punching
Assembly or packaging
Choosing a factory that handles these in-house saves you from managing multiple vendors and ensures consistency in quality and scheduling.
6. Quality Assurance and Certifications
Reliable extrusion factories invest in quality control systems to detect and eliminate defects before the product reaches your facility. Look for the following signs of a commitment to quality:
ISO 9001 certification
Inspection reports with every batch
In-process checks for dimensions, surface finish, and strength
Material traceability systems
Third-party testing if required
Make sure the factory’s QA/QC process aligns with your standards, especially if you’re operating in highly regulated industries like aerospace, defense, or healthcare.
7. Production Lead Time and Logistics
Timing is everything. Delayed shipments or missed deadlines can halt your entire operation. Ask each extrusion factory about their average production lead times and how they handle urgent orders.
Important points to clarify:
Typical lead time from order to delivery
Flexibility during demand spikes
Packaging standards to protect extrusions during transit
Export capabilities (if you’re ordering internationally)
A factory with a strong logistics network and experienced shipping team can deliver your parts on time and in perfect condition — wherever you are.
8. Customer Service and Engineering Support
Excellent communication is essential when working with custom components. The best aluminum extrusion factories act as partners, not just vendors. They provide engineering assistance, design feedback, and responsive support throughout your project.
Signs of a supportive partner:
Dedicated account manager or project coordinator
Willingness to collaborate on design optimization
Clear communication and regular updates
Fast response time for inquiries or technical support
9. Reputation and Client Feedback
Don’t take a factory’s word for it — see what others have to say. Reviews, testimonials, and referrals can provide insight into a factory’s reliability and overall customer satisfaction.
Look for:
Client case studies or success stories
Verified testimonials
Online ratings or third-party reviews
Industry awards or recognitions
If possible, schedule a factory visit or request a virtual tour to evaluate their operation, cleanliness, staff expertise, and equipment condition.
10. Sustainability and Environmental Practices
As industries worldwide embrace sustainable practices, it’s increasingly important to work with factories that prioritize the environment. Many leading aluminum extrusion factories now focus on:
Using recycled aluminum billets
Energy-efficient machinery
Zero-waste or low-waste production models
ISO 14001 environmental certification
Not only does this support global sustainability goals, but it can also enhance your brand image and help meet green building certifications (LEED, BREEAM).
Bonus Tip: Consider Long-Term Scalability
If your business plans to scale, your extrusion partner should be able to grow with you. Ask whether they have plans for expansion, newer equipment, or increased capacity. A factory that can accommodate both your current and future needs ensures continuity and avoids future disruptions.
Conclusion
Choosing the right aluminum extrusion factory is more than just comparing prices. It’s about finding a reliable partner with the right capabilities, quality standards, customer support, and industry expertise to meet your project’s specific needs.
From die design and alloy selection to post-processing and logistics, every detail matters. When you align with a top-tier factory that understands your goals, you’re not just buying aluminum extrusions—you’re investing in efficiency, innovation, and long-term success.
Take the time to evaluate your options carefully, ask the right questions, and look for a partner that brings both technology and trust to the table. With the right factory by your side, the possibilities for your project are virtually limitless.